Optimizing the Wet End Management in Paper Making: Strategies, Techniques, Innovations, and Best Practices
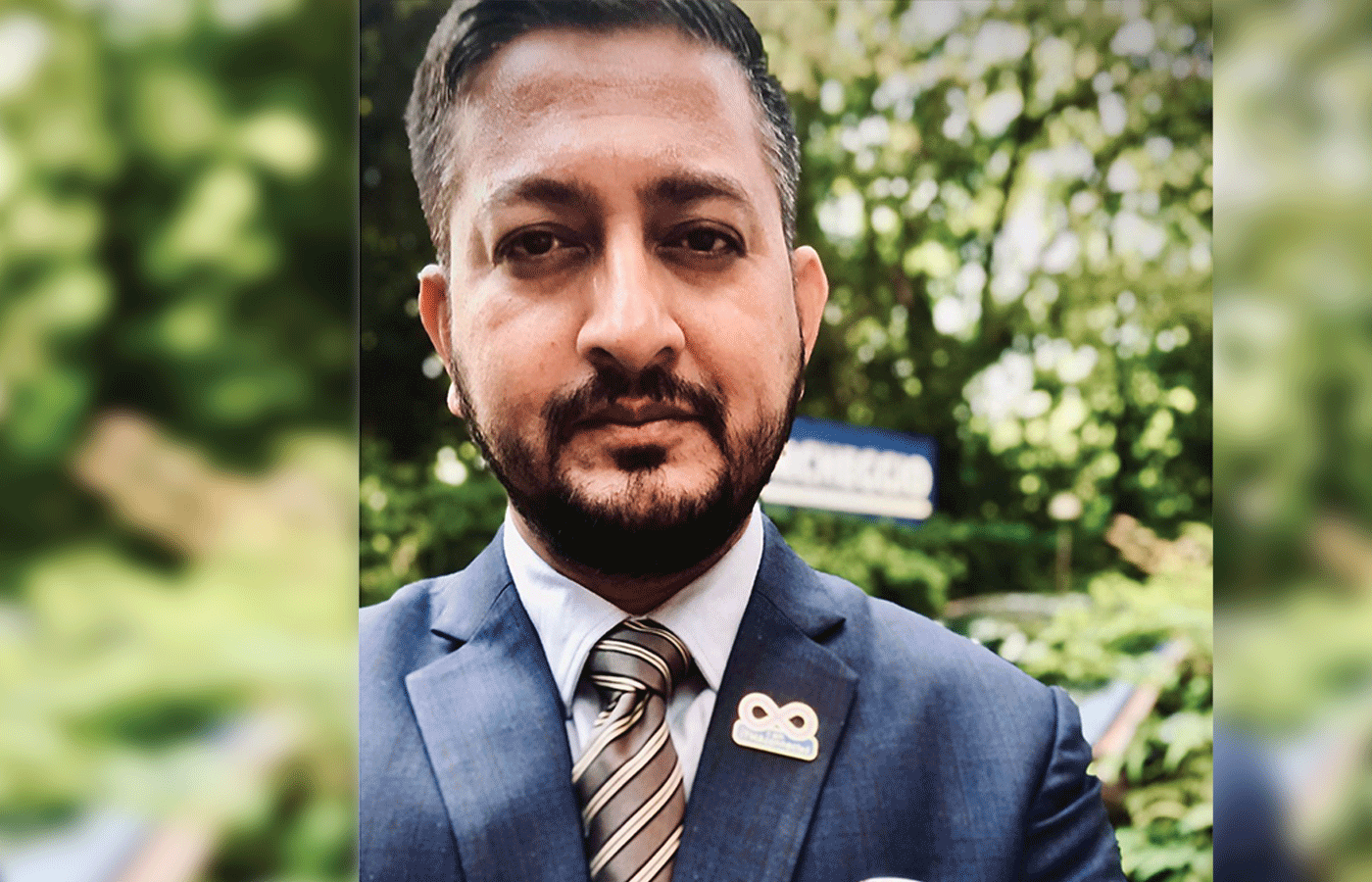
Abstract: The wet end of paper making is a critical stage that impacts product quality, resource utilization, and environmental sustainability. This article provides a comprehensive exploration of wet end management, covering modern strategies, innovative techniques, recent advancements, and best practices to maximize efficiency, enhance paper properties, and minimize waste in the paper-making process.
Introduction: The wet end represents the foundational phase of paper production, where fibers, chemicals, and water converge to create pulp. Achieving optimal wet end management is vital for consistent quality and economical paper manufacturing. This article delves deeply into the complexities of wet end optimization, offering insights into various dimensions of this critical process.
- Fiber Preparation and Quality Enhancement: Modern fiber preparation involves cutting-edge techniques such as enzymatic modification and advanced pulping methods. Enzymes like cellulases and hemicellulases are used to enhance fiber flexibility and pulp drainage. Selective pulping approaches, such as pressure-resistant pulping, improve fiber quality while minimizing energy consumption.
- Chemical Addition and Mixing: Precision in chemical dosing and mixing is pivotal for retention, drainage, and overall paper quality. Employ state-of-the-art automated dosing systems equipped with AI-driven algorithms and predictive analytics. Incorporate advanced mixing technologies like inline sonication or microfluidic systems for unparalleled chemical dispersion.
- Forming Section Optimization: Efficient water removal in the forming section is pivotal for paper formation and uniformity. Utilize advanced hydrofoils with adjustable geometries for fine-tuned water removal. Innovative vacuum box designs integrated with smart sensors optimize drainage efficiency while minimizing fiber mat variations.
- Press Section Enhancements: Dewatering efficiency in the press section is revolutionized by advanced shoe press designs equipped with real-time pressure control. Nanotechnology-enhanced fabrics offer higher dewatering efficiency and improved paper strength. Utilize AI-driven algorithms to optimize controlled nip settings for maximum water removal.
- Drying Efficiency: Energy-efficient drying is essential for sustainable paper production. Recent innovations include thermally efficient steam-heated dryers with integrated heat recovery systems. Deploy advanced moisture profiling systems using IoT sensors for real-time data, enabling dynamic control algorithms to achieve unparalleled uniform drying.
- Process Monitoring and Control: Real-time process monitoring is facilitated by IoT-connected sensors and cloud-based analytics platforms. AI-driven algorithms process data streams to provide actionable insights for timely adjustments. Blockchain technology is used for secure data sharing and traceability across the supply chain.
- Water Management and Sustainability: Sustainability is driven by cutting-edge water management technologies. Closed-loop water systems are integrated with AI-driven predictive analytics for real-time water quality monitoring. Advanced water treatment processes, such as electrocoagulation and membrane bioreactors, ensure efficient recycling and minimal environmental impact.
- Fiber Refining: Modern fiber refining combines high-precision mechanical refining with advanced chemical treatments. Nanocellulose-based additives improve fiber bonding and strength. Integrated refining control systems utilize machine learning algorithms for dynamic refining intensity adjustment.
- Operator Training and Maintenance: Skilled operators are empowered through immersive virtual reality (VR) training modules. Predictive maintenance employs machine learning models trained on sensor data for proactive equipment maintenance and enhanced reliability.
- Data Analysis and Continuous Improvement: Leverage big data analytics and machine learning for deep process analysis. Implement digital twins of the wet end for simulation and optimization. Continuous improvement is facilitated by collaborative platforms that enable sharing insights across teams and facilities.
- Conclusion: Optimizing the wet end management in paper making is a multifaceted endeavour that embraces the latest technologies, innovations, and methodologies. By integrating state-of-the-art solutions, process optimization, skilled workforce management, and data analysis, paper mills can achieve unprecedented levels of productivity, resource efficiency, and paper quality. This commitment positions them for sustained success in a competitive industry, where wet end management is pivotal for shaping the future of efficient and sustainable paper production.
Below stated a summary of recent innovations and their applications in optimizing the wet end management in paper making:
Innovation |
Application in Wet End Management | Benefits |
Enzymatic Fiber Modification | Enzymes like cellulases, hemicellulases | Enhanced fiber flexibility, improved drainage |
Pressure-Resistant Pulping |
Selective pulping techniques | Higher fiber quality, reduced energy usage |
AI-Driven Chemical Dosing |
Automated dosing systems with AI algorithms | Precise chemical dosing, reduced waste |
Advanced Mixing Technologies |
Inline sonication, microfluidic systems |
Uniform chemical dispersion, efficient mixing |
Adjustable Hydrofoils |
Forming section water removal enhancement |
Fine-tuned water removal, improved formation |
Smart Vacuum Boxes |
Innovative vacuum box designs with sensors |
Optimized drainage, minimized fiber mat variations |
AI-Controlled Shoe Presses |
Real-time pressure control in press section |
Improved dewatering, reduced energy consumption |
IoT-Enabled Moisture Profiling |
Moisture profiling systems with IoT sensors |
Real-time drying control, minimized defects |
Blockchain Data Sharing |
Secure data sharing and traceability |
Transparency in process data and quality |
Advanced Water Treatment |
Electrocoagulation, membrane bioreactors |
Efficient water recycling, minimal impact |
Nanocellulose Additives |
Fiber refining with nanocellulose-based additives | Enhanced fiber bonding, increased strength |
VR-Based Operator Training | Virtual reality training modules | Enhanced operator skills, reduced downtime |
Predictive Maintenance | Machine learning-based maintenance | Proactive equipment maintenance, reliability |
Big Data Analytics | Data-driven process analysis |
Continuous improvement, optimized processes |