Paper Mill’s water circuit closing, Process challenges and its importance.
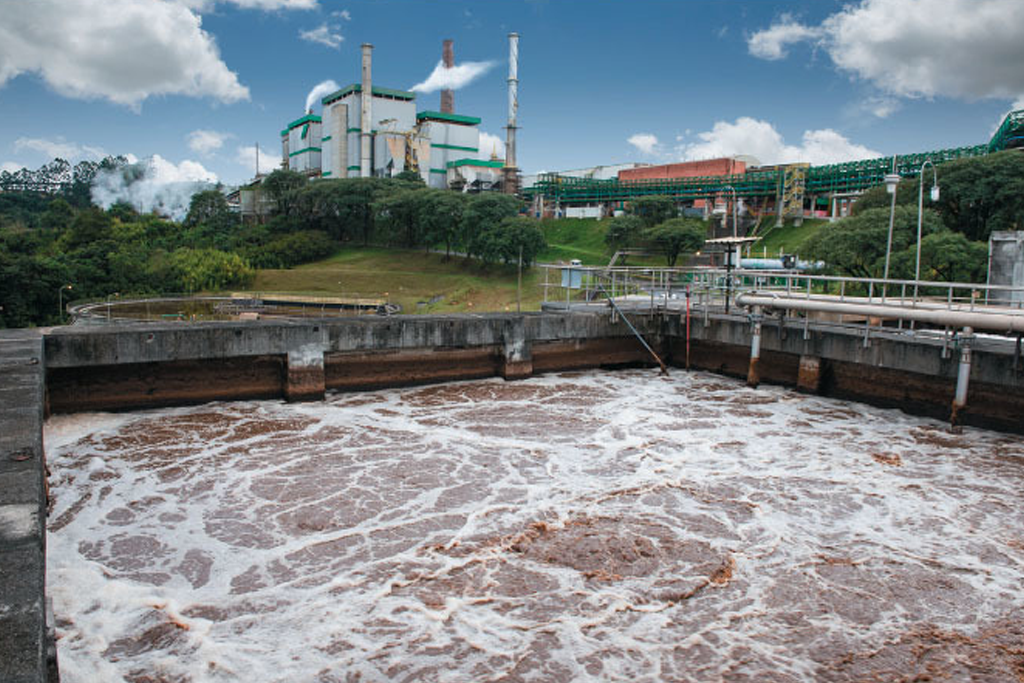
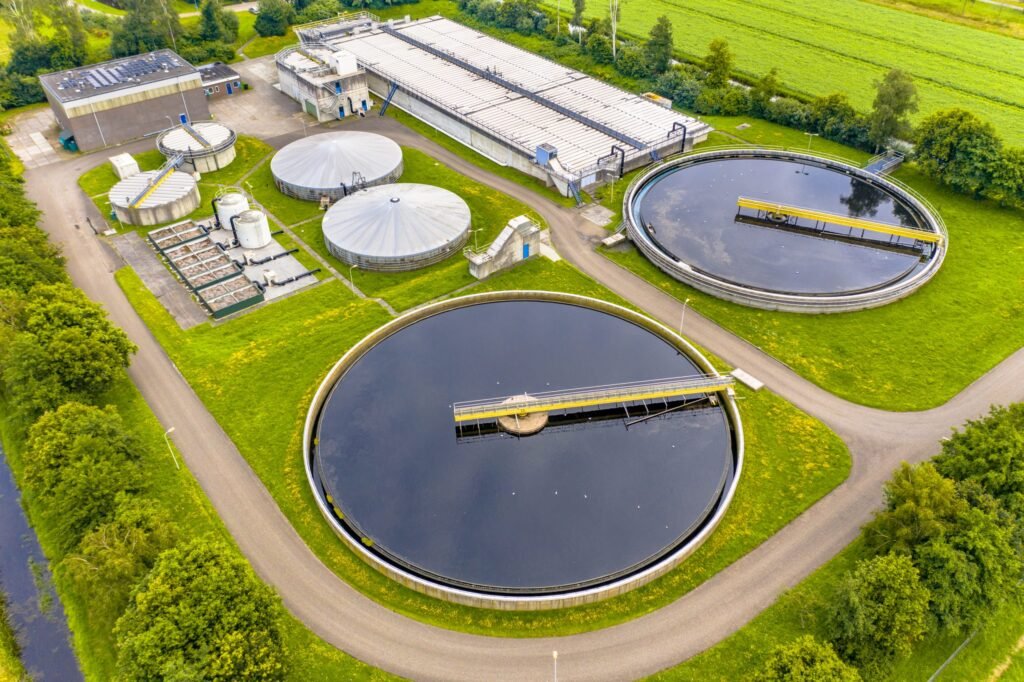
Receiving continuous pressure form Department of Environment in terms of Zero Liquid Discharge (ZLD) and to optimize power consumption, many of the Paper Mill are subjected to close their water circuit of Papermaking process especially in Bangladesh. This article will discuss the portion of related matters and possible remedy for the said topic.
Positive impact of water circuit closer in Papermaking process
- Less water consumption.
- Less fresh water pretreatment.
- Lower volumes to effluent treatment. The treatment plant can be built smaller (lower investment and operational costs).
- Contaminants are more concentrated which allows often higher removal efficiency and thus lower emissions.
- Increase of production not hindered by exceedance of permitted flow.
- Decreased fibre in filler losses that means increases total retention of the mill but not first pass retention.
- Elevated process temperature which leads to improved dewatering of the paper web.
The most common unwanted side effects due to water circuit closer in Papermaking process are:
- A surprising decrease in the brightness of paper.
- Problems related to the water-repellent properties of paper that means lowering size or increases sizing chemical dosage level.
- Unexpected changes in a paper’s strength.
- Occurring slime holes and spots in paper.
- Increase the rate of felt-filling and related deposits.
- Decrease the efficiency of retention aids.
- Increase paper break and affect the smooth operation of the paper machine.
- Build-up of (suspended) solids.
- Build-up of organic and inorganic substances.
- Increase of odour problems due the build-up of organic substances.
- More complicated processes.
- Risk of lower product quality, e.g. concerning brightness, strength, softness, porosity
- Corrosion problems.
- Increased use of additives.
- Clogging of equipment.
- Scaling and slime forming.
- Increased temperature of the process water.
Colloids and White water
Most of the Papermakers are familiar with the term “White water” or some time called “backwater”. White water generated from papermaking process while forming wet paper web. White water composition can be varied significantly depending on its coming sources and the type of raw material used. Excluding existence of valuable fines and fillers, white water contain broad varieties of impurities.
There are two main groups of impurities: the so-called “anionic trash”(=real or colloidal dissolved anionic polymers) and the so-called “pitch” (= non-ionic hydrocolloids of different origins).
These substances can originate from various areas, such as:
- Deinking: sodium silicate
- Filler dispersion: poly acrylates, polyphosphates, etc.
- Coated rejects: starch derivatives, binder etc.
- Pulp: organic acids, hemicelluloses, resins
- Fresh water: humic acids
Moreover, it also come from chemicals that are intentionally added during the papermaking process.
For better understanding easing the detail of concepts-
Running Conditions
Some key variables associated with white water composition, including fine-particle retention, charge demand and the content of entrained air these would be monitored by installation of online sensor or offline laboratory testing. Such type of monitoring can be used as a basis for optimization of chemical dosage, maximize paper quality and minimize production cost.
However components of white water can be classed as inorganic, organic, or biological. They also can be classed as dissolved or finely suspended. There are a great many different materials that can be present in white water, and importantly pair-wise interactions (similar charge repeal each other) between them make Papermakers face a challenging job when seeking to identify optimum running conditions of paper machine and also the quality of end product. For example; over dosing of negative charge belonging chemicals decreasing first pass retention, sizing, and other production goals. To overcome this problem charge scavenger or fixing agent can be added to tie up the excess anionic charges.
Enrichment
White water becomes reused multiple times recurrently in a modern and closed water circuit paper machine system. Each cycle of use provides another opportunity for materials to become dissolved, emulsified, or removed as small particles from the surfaces of fibres or from other additives to the process.
If any accumulation of “substantive material” such as Na2+ , Mg2+ and Surface-active materials (such as soaps) and finely suspended materials of any pair of positive and negative ions reaches its solubility limit, then one can expect that a precipitate may form. If the precipitate is inorganic then scale will form at the surface of different equipment’s. In that case inside pipe dia, vacuum suction area will decrease and other forms of problem may occur. Another accumulation of salt content will affect the performance of additives. Moreover, Salt also reduces the swelling of fibres, an effect that tends to slow down refining and reduce the strength of the resulting paper. The white water also tends to become more corrosive towards metals with increasing concentration of simple ions. Consequently, in case of fresh water salt removal is an important issue. But in case of Bangladesh most of the paper mill ignore the process of salt and iron removal. In that case would better to introduce WTP for process water.
Whiter Water Component in Recycling Cellulose Fiber (RCF) Papermaking:
In Recycled paper mill, white water contains ink particle, surface active material of nonionic surfactant and fatty acid soap followed by addition of Calcium salt. The carryover of surface active material increases the level of foam and make it somewhat more difficult to retain fines and to achieve hydrophobic sizing of the paper. The positive aspect of deinking operation from the stand point of white water management is that the resulting fibers can be in some respects, cleaner than primary pulps that are produced on site. Much of fines content, fillers, extractives and soluble hemicellulose components trend to be separated from the filterable solids and removed during the washing operations associated with de-inking. Therefore, washing is very important in de-inking operations. That means higher the efficiency of washing better in favor of process operation.
When coated broke or coated paper is in recycling then certain binder and latex can be released into the water phase and that certain binders can have a tendency to deposit into papermaking equipment similar to wood pitch. Importantly, if the flakes of coating fail to re-dispersed in re-pulping then dusting and blemishes can be observed in the paper product. In coated recycled paper, coating derived phosphate or acrylate dispersant having tendency to increase the cationic demand of the system, consequently creating it more challenging it to achieve the desired level of first pass retention as well as increasing solid content of white water.
Envelop, Magazines, are usually labeled by attaching dry stamp which contain adhesives are called stickies (another source of stickies is glue binded book) and it pass into papermaking operation and enter in a paper machine system. Some time it exist as a major component of white water solids, their adhesive nature can cause bothersome deposits in press felt, Uhlebox , dryer surface, dryer screen, and other parts. It hampers the quality of paper, machine run ability and other heat transfer issue in case of dryer surface and screen deposition in RCF process. Various mechanical separation and chemical application technique could take to control such problem. There are possible problem solving strategies that would include but not limited to-
- Mechanical cleaning with sorters and cleaners; process include screenings like vibratory screen, corase screen, fine screen , plastic or junk separators, HDC, LDC, hot dispersing etc.
- Fixation within paper and therefore discharge via paper.
- Masking or removal of stickies ; for example using talc , stickies control agents etc.
- Cleaning of circulating water.
- Optimizing the dosage of de-inking chemicals.
Chemical additives as a source of white water component
In case of printing grade 10-25 % filler used, therefore fillers have a relatively large impact on the properties of white water. Filler particles are too small and have large surface area and are efficiently retained by filtration of cellulosic web. Thus depending on the effectiveness of retention aid programme, there is a good chance that much filler will be lost to the white water and they accumulate in the white water.
Even though, additive has a charge attraction to cellulosic fiber but if dosage level exceeds the saturation level of fiber surface, then there is possibility for significant build up in white water. For example, depending on the surface area of furnish (affected by refining and type of filler used) the addition of higher quantity of cationic starch merely results that build at white water contributing to foam and bacterial growth. The BOD also increased due to the presence of unretained starch. Moreover, excess addition of cationic material than its requirement then retention become less efficient and the system likely to be foamy and slow dewatering will occur. Therefore, dosage optimization, anionic trash catching, dosage location with retention achievement is an important issue for papermakers.
Significantly Sizing is the goal where is to absorb the sizing agents (ASA, AKD, resin products) efficiently on the surface of fibers and fine particles. At the same time fibers, fillers, and fines particles need to be subsequently retained efficiently by retention aids as the paper is formed. But the hating or hydrophobic nature of sizing additives implies that they can contribute to tacky deposits while present in white water. Defoamer products also share the same bad habits because of having hydrophobic and tacky character consequently they have tendency to deposit on papermaking equipment.
Papermakers usually should maintain minimum use of surface active material to the wet end because of their concern about performance of sizing agent, the generation of foam, and to some extent of paper strength properties. If the related data’s are obtained by testing at good running and good product quality situation, then this would help to solve problem at bad conditions of process and product quality.
1. Auer-Welsbach, C. “New methods of fresh water preparation and effluent purification in pulp and paper mills,” Wochenbl. Papierfabr. 102 (8): 293- 4,296 (1974).
2. Stevenson, S., “With a zero-effluent mill Millar Western will meet the stringent Saskatchewan standards,” Pulp Paper Can. 91 (4): 16-18 (1990)
3. Lindholm, G. “Reduction of fresh water consumption in pulp and paper production,” Paperi Puu 80
(4): 260-263 (1998).
4. Norris, P. “Water reclamation operations in a zero-effluent mill,” Proc. TAPPI 1998 Internal. Environ. Conf., Vancouver, BC, TAPPI Press, Atlanta, 1045-1050 (1998).
5. Jahren, S.J., Rintala, J.A., and Ødegaard, H. “Evaluation of internal thermophilic biotreatment as a strategy in TMP mill closure,” Tappi J. 82 (8): 141-149 (1999).
6. Stebbing, E. “Potential of fungal culture filtrate treatment to reduce extractive levels in newsprint mill white-water systems,” Pulp Paper Can. 100 (3): 46-49 (1999).
7. Gubelt, G., Lumpe, C., Verstaeten, E., and Loore, L. “Toward zero liquid effluent at Niederauer Mühle – The validation of two novel separation technologies,” Paper Technol. 41 (8): 41-48 (2000).
8. Pauly, D. “Kidney technology for whitewater treatment,” Paper Technol. 42 (8): 29-36 (2001).
9. Robinson, M., Blackwell, B., Dare, P., Frost, N., Lloyed, J., Malmqvist, A., and Slade, A. “Upgrading TMP whitewater for internal recycled: Biological and physicochemical treatment and effects on pulp quality,” Proc. APPITA Gen. Conf., April 30-May 2, 2001, Hobart, 1, 167-174 (2001).
10. Hamm, U., and Göttsching, L. “Wastewater-free papermaking – What consequences to expect?” Wochenbl. Papierfabr. 130 (4): 229-235 (2002).
11. Laine, J.E., and Bourgogne, G. “A review of the effects of reduced water consumption on the wet end of the paper machine and the quality of paper,” Proc. Scientific and Technical Advances in Wet End Chemistry, Vienna, Austria, May 22- 23, 2002, Pira International, Leatherhead, Surrey, UK, Paper 1 (2002).
12. Jahren, S.J., Rintala, J.A., and Ødegaard, H. “Aerobic moving bed biofilm reactor treating thermomechanical pulping whitewater under thermophilic conditions,” Water Res. 36 (4): 1067-1075 (2002).
Article by:
Md. Moniruzzaman
Master of Engineering in Pulp and Paper Technology, AIT, Thailand
Master of Science in Applied Chemistry & Chemical Engineering, Islamic University, Bangladesh
Email : monirait@yahoo.com
Cell: +8801759685886